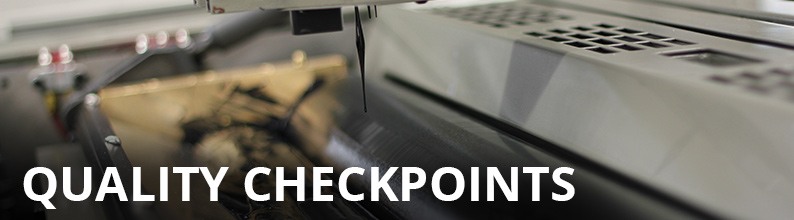
33 Quality Checkpoints: Follow the Life Cycle of your order
Pre Press Department: 15 Checkpoints
From our file prep checks to imposition, we do everything we can to guarantee that your pieces are printed accurately and professionally.
- Resolution Review
- Size Verification
- Bleed Verification
- Safety Zone Review
- Human verification of artwork matching the order specs
- Color mode review, including an evaluation for major color shift
- Check for white overprint
- For orders requiring post-press work; verify scores, die-cuts, folding and mailing clearance
- Preflight press ready files and final human inspection
- Electronic verification of the files submitted to next work area
- Electronic preflight checks: fonts, vector images, raster images, resolution, and color modes
- InRip trapping for optimal print registration
- Human verified order specifications
- Human inspected order output
- Human inspected order plating process
Press, Cutting & Bindery: 10 Checkpoints
Quality continues all the way through the production process. From our state of the art printing press to human inspection of your piece at every point during printing.
- Closed Loop Color to automatically achieve and maintain the correct color levels
- Strict procedures and guidelines that define and control the printing process to save time and money
- Constant inspection of the printed product during the make-ready and run process for consistent quality and pinpoint errors
- Color Density
- Examine the printed sheet for proper density of all four colors
- Check for proper trapping of the inks
- Confirm that color breaks are correct
- Check color match consistency on multiple up elements
- Compare illustrations of print to originals supplied for color fidelity if applicable
- Registration
- Check each color image and screen build element for internal register
- Check the sheet for correct backup of images, cuts, scores, etc.
- Verify that bleeds extend beyond the trim marks and insure that no words or pictures are being cut off
- Stock
- Verify the paper stock is what is requested in weight, color and brightness
- Overall impression
- Inspect the entire press sheet, looking at the pictures, type, screens to make sure they are consistent
- Compare all copy on the sheet to the blueline
- Verify that the correct quantities are being run
- Check for missing elements and copy changes if applicable
- Check type carefully for broken letters and imperfections
- Examine sheets for hickeys, blemishes, pinholes, mottling, or ghosting and anything unusual
- Verify all cards are cut accurately and in a square format
- Verify final size and bleed is trimmed off
- Human inspection to ensure consistent quality and help prevent errors
- Equipment preventive and predictive maintenance programs to maintain quality and to prevent late deliveries due to unscheduled downtime
Quality Assurance & Shipping: 8 Checkpoints
Our final quality inspection on all products and accurate packaging is all part of making sure your product is up to our standards and ships on time.
- Quality checkpoints at every stage in production performed by trained Quality Assurance Specialists to ensure satisfaction
- Final product is inspected prior to leaving our facility. If an issue is detected they are fixed before the order ships to ensure customer satisfaction and a timely delivery
- Constant improvement in processes and solutions to prevent the same issues from reoccurring
- Human inspection on all printed pieces for any product
- Boxes designed to fit specific quantities for optimal delivery
- Electronic verification of delivery address and ship mode
- Sign off required by a shipping clerk for every job to ensure customer satisfaction
- Department works 24 hours to ensure on-time shipping. Shipping systems are integrated with our databases to provide real time tracking numbers to let our customers know when their order ships